Processing
Processing
Collecting is not Recycling!
Recycling is not accomplished by simply collecting a material at curbside.
That material must be successfully recovered from the rest of materials collected, it must have a market willing to accept that materials, and the market must be able to process the material into something useful that consumers are willing to buy in hopes to use and repeat the whole process all over again.
In this section, we discuss our approach to processing the materials we collect and how our high tech material recovery facility is able to recover and market 96% of all materials collected.
Our systematic approach to apply pre-defined treatment methodologies to maximize recovery and value of the commodities collected is fundamentally different than most other operations in our industry.
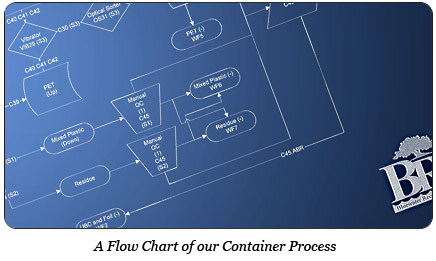
Material Recovery Facility
The Balance Between Purity and Efficiency
The traditional approach to material sorting has been mainly driven by people lined around conveyors manually separating different commodities to meet market demands.
This approach was rudimentary and effective when only five materials were collected curbside. Applying this approach to today’s material mix is accepting that material quality is not important, high sorting costs are acceptable, and repetitive strain injuries are normal. We do not support this approach to processing.
While the Association is proud of its past developments in the Material Recovery Facility, the future of our industry demands higher throughput and a higher quality standard with a broader mix of materials. The ever changing packaging stream makes it a necessity to use technology to assist in the sorting activity, as our people cannot physically and mentally process what is presented to them today in a speed necessary to be effective.
One example is in the early 90’s, a PET bottle was essentially a 2L soft drink container. They were easy to identify and quantities were manageable to manually sort after some basic screening. After the Walkerton water incident, single serve PET water bottles proliferated the market place. The impact at the Material Recovery Facility was an increase in bottles managed from 500,000 per year to over 25 million.
It is impossible to manually sort this volume and maintain quality without mechanical assistance. The use of people to manually sort materials resulting in repetitive strain injuries is not sustainable. The average human hand can effectively pick 1,500 pieces an hour. Our optical sorter can do so at up 400,000 pieces per hour.
The comparison is not even close.
The latest technological advances in our industry have enabled us to effectively change the treatment approach of recyclables where technology does the sorting and our people focus on quality.
Facility Tour
How It Works
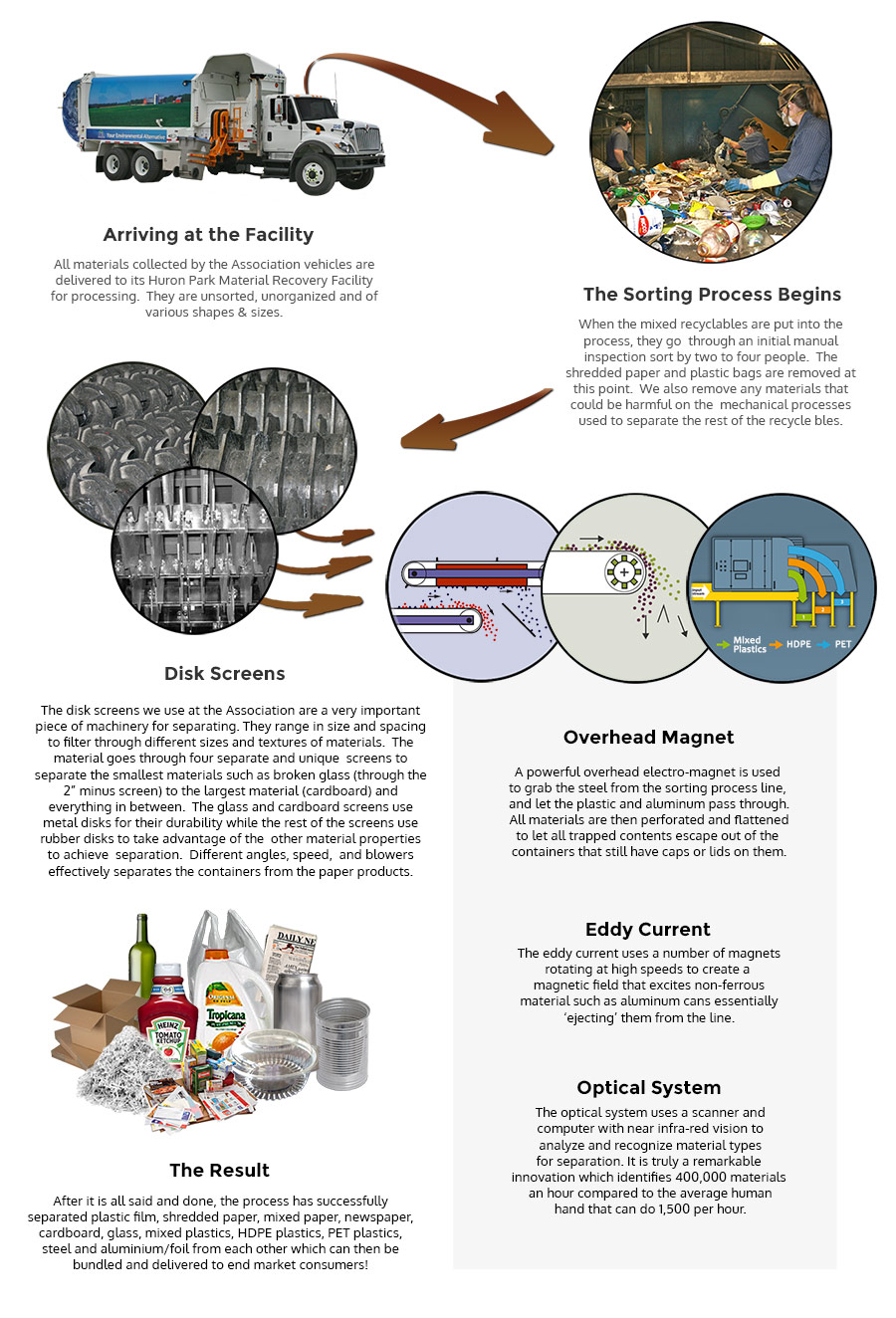
End Markets
Where It Goes!
The Association takes great care in deciding what materials can be accepted in its recycling program in order to meet its commitment to member municipalities that everything collected will be recycled. As such, we use a three step approach in determining material acceptability.
For one, unless the “new” material has three solid established markets within reach it will not be considered. We do this to ensure that we will have a sustainable long term market in place in order to be able to guarantee you that all recyclables collected at curbside will be recycled.
Secondly, it has to make economic sense to collect, process and ship the material. We have a fiduciary duty to the taxpayer to keep waste management cost affordable. Unless you believe that recent fuel increases are no big deal because you can afford them, we like to keep the recycling costs to a minimum.
Lastly, we want to make sure that recycling a material will make a significant impact on the environment to justify the infrastructure and investment that will be required to handle the material differently than it is today. Often, we look to see if consumers have alternative choices available to them that could be used to avoid the material in the first place to determine the urgency and viability of adding the material.
With this approach we are able to objectively evaluate the potential materials available for diversion. We can add materials to the program ensuring they will be recycled while keeping costs affordable for the end user.
This enables us to guarantee that what we collect from you will be recycled. Over 96% of everything collected makes it to an end market to be made into new products. To see 'what becomes what', click here.
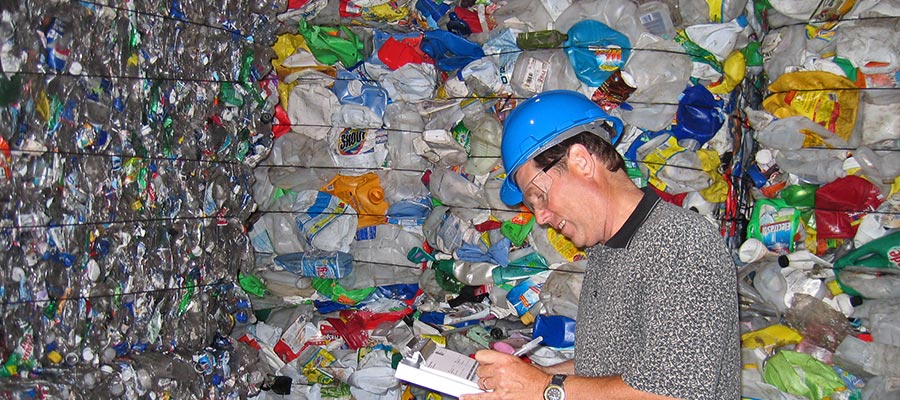